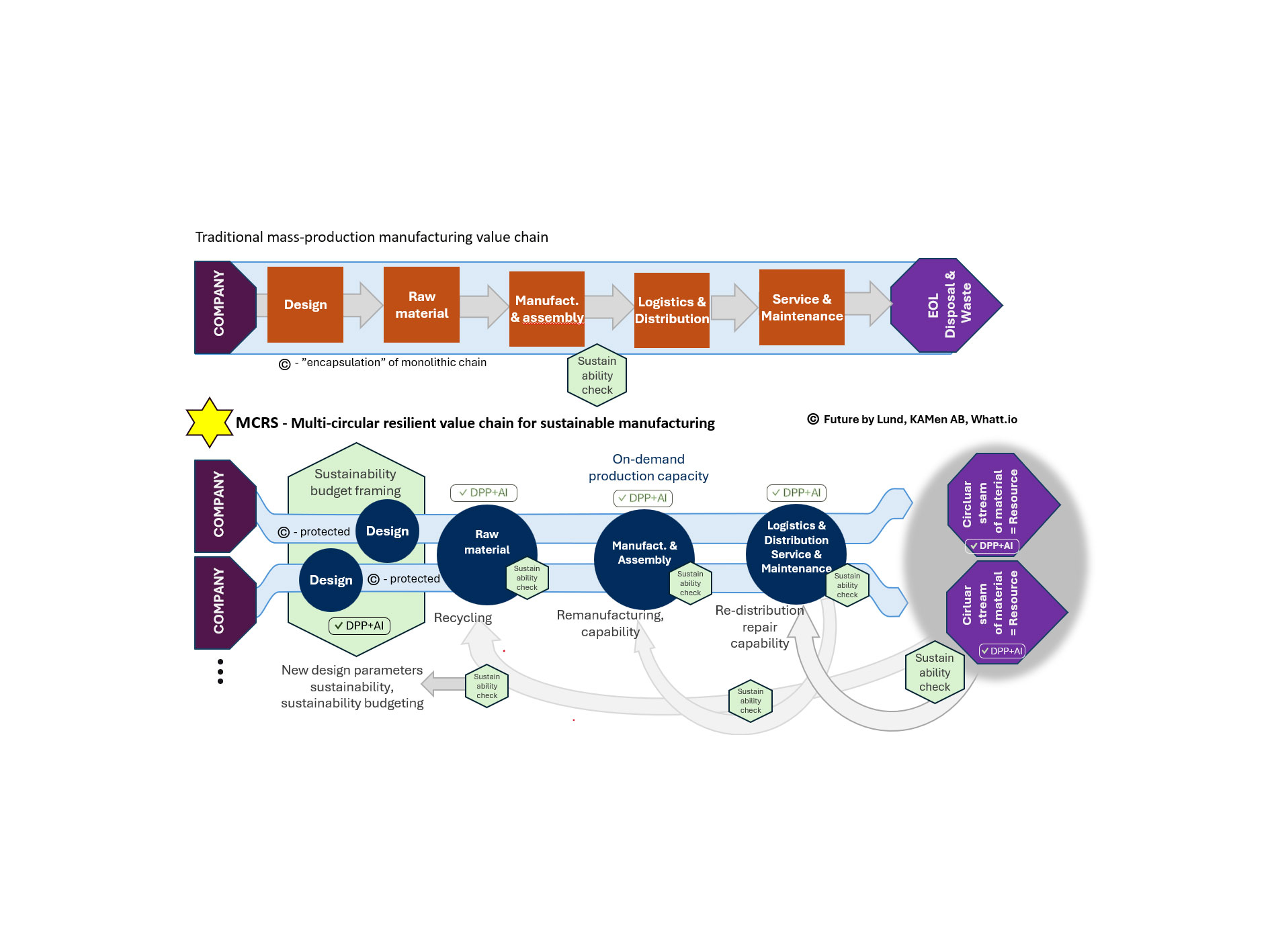
MCRS: Sustainable manufacturing industry tested in Lund
Climate change, resource scarcity and increased environmental requirements mean that the manufacturing industry faces significant challenges that require a radical transformation. The solution could be a production that is more on-demand and circular, where manufacturing matches demand, where products and components can be repaired and replaced, and where resources are reused and recycled as efficiently as possible. But how will it be done in practice? In a new project, Future by Lund and partners will explore how we can build a system demonstrator where the goal is not only to see how the industry can become more sustainable and circular, but also more local and resilient.
In cooperation with Lund University, KAmen Nordic, Whatt.io, Lostboyslab and Infinite Acoustics Future by Lund will work in the planning project MCRS (Multicircular and Sustainable Manufacturing Industry) to explore how we can create a system demonstrator to help manufacturing industries and companies make a green transition in line with the EU regulatory framework and new circular economy standards
The manufacturing industry is global and complex, and recent years have shown that it is also vulnerable to disruptions caused by global crises such as pandemics, geopolitical conflicts, and financial and climate-related disasters. All this adds up to the fact that a major change for manufacturing, business and consumers is to be expected.
This is a transition that requires not only technological innovations, but also changes in behaviour, business models, service development, training, regulations and market structures. To achieve this, cooperation across knowledge and industry boundaries is needed. In such a broad and complex challenge, many actors, sectors and disciplines need to work together — as is already happening on the Future by Lund innovation platform, where actors from universities, industry, cities and organisations unite in an ecosystem. Here, the existing knowledge of the project partners can be matched against the innovation platform's extensive network and create knowledge exchanges and development across the board.
A key competence in the construction of a new system demonstrator and in the planning project are solutions around the Digital Product Passport (DPP) driven by EU regulatory work. Equipping products with DPP can ensure full traceability and transparency over the entire product lifecycle, from raw materials to recycling and recirculation. To lay a foundation for this, the ambition is to create and connect material databases, industrial actors, materials research, user design and recycling in a system demonstrator, thus laying a systemic foundation for scalable manufacturing models with a focus on circularity and resilience. The DPP will increase traceability and enable verification of materials and components, connection to various services for example repairs, which increases the life of products and generates new business. At the same time, by developing and integrating AI and data analytics on the data created from DPP throughout the multicircular value chain, one can build the ability to anticipate and respond to disruptions that may occur throughout the process.
An important part of the planning project is to examine the work done through the production chain developed by Whatt.io, Lostboyslab and Infinte Acoustics to build a system demonstrator based on these experiences. Infinite Acoustics, IAc, manufactures high-end speakers that, using DPP, have a verified lifecycle model. Manufacturing takes place locally and a large number of components are produced via additive production at Lostboyslab. The components produced via additive manufacturing are part of a multicircular flow where residual materials from various industries such as plastics, rubber and forest fibres can be mixed with materials from IAc. All this is done in a Swedish local production chain. Whatt.io participates through its knowledge and ability to use DPP.
To create a systems demonstrator, the project will build on this knowledge to demonstrate and test integrated solutions and explore how technologies such as DPP, AI and additive manufacturing can be integrated into a coherent solution for sustainable manufacturing The ambition is to be able to iterate solutions to test them in real-world environments and production chains, ensuring that they are not only technically feasible but also practically usable, scalable, implementable and transferable to others manufacturing industries. After optimizing the production chain, more players can be connected to create a larger functioning ecosystem.
A central part of the project is to build opportunities for iterative working methods that involve constantly evaluating and improving the solutions, based on feedback and data from real-world tests. It is also important to bring in the circular model already at the design stage.
The project operates within the call “Impact Innovation - System Demonstrators for Sustainable Manufacturing Industries of the Future - Step 1". Stage 1 is primarily a planning phase, and a possible stage 2 would involve the possibility of building a system demonstrator with many partners.
MCRS - The Multicircular and Sustainable Manufacturing Industry
Project Financing: approx. 1,5 million SEK
Financier: Vinnova
Project Manager: Lars Mattiasson and Anders Trana
Project Time: 2024-10-14 - 2025-08-30
Project partners: Future by Lund, Lund University, KaMen Nordic, Whatt.io, Lostboyslab and Infinte Acoustics.