DPP shows the way for the future of manufacturing
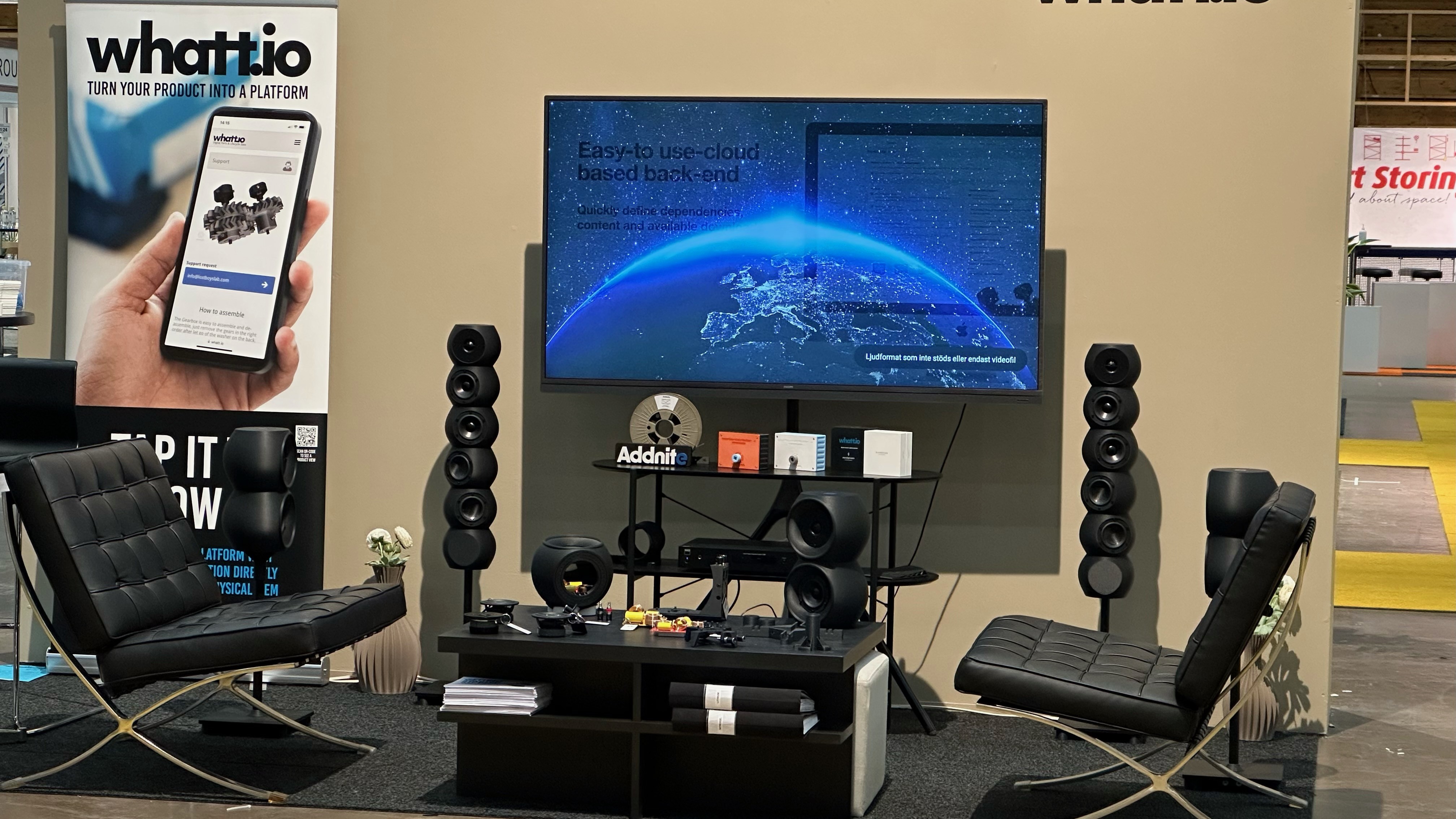
The DPP can be described as the digital twin of a product and can contain information on everything from materials, manufacturing and transportation to repair and recycling opportunities. There is, of course, the possibility of adding additional information, such as instructions for use, service and who has used the product. DPP in the simplest form can mean that the product is provided with a QR code that is read by, for example, a mobile phone or an NFC tag that is like a small memory in the product and can be read by radio signals, most simply via a mobile phone. There are also more advanced and interactive solutions. An advantage of the information available through the DPP is that it can be updated and replaced afterwards — especially practical for long-life products.
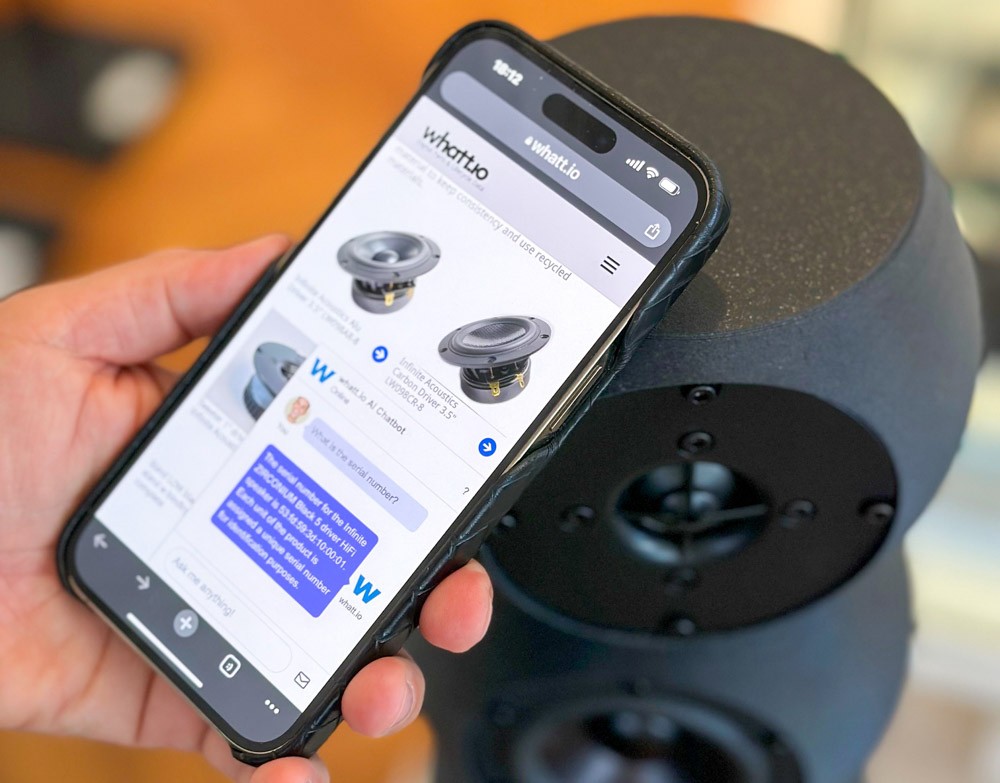
Stefan Larsson on whatt.io worked early on to make digital product catalogs for the construction industry so that both furniture and building products would be available digitally to help architects and engineers, for example, in their work.
- This is where the idea was born to identify components and products in such a way that users have access to maintenance information, service, support and spare parts, says Stefan Larsson. Back then we called this the Product Lifecycle Platform — but after the EU started talking about DPP, Digital Product Passport, we also use that name.
Now, whatt.io works with several variants of DPP, but also has complete solutions with “DPP as a service”, providing a platform where manufacturing companies can quickly get up and running to meet upcoming EU regulations.
- We hope to be involved in building great digital tools for companies so that DPP is not only a whip but also a carrot for companies. Through DPP it is possible to post it so that the customer, when “flipping” the product, gets in touch with the support and can buy parts and accessories directly. In this way, you can build a good customer relationship and build loyalty with the brand.
It is not yet clear how the EU rules and recommendations will be framed, and by the project Cirpass-2 whatt.io is involved in designing the regulatory framework. Part of the project looks at what authorities, producers and users demand and builds a standard for how to read and write the DPP and what data should be included. The second part consists of pilot projects where DPP is tested in practice.
- Being part of the project is also a way to be involved in changing the world. As an entrepreneur, I know that companies only change their minds when they have to. In this work, we can find what could be the impetus for more people to become environmentally friendly and circular.
The first products with legal requirements for DPP are expected to be batteries, small electronics and textiles. The intention of the rule changes is to create a more resilent, circular and sustainable society in which the DPP becomes a catalyst.
- If you want to extend the life of the product, information about the product is an important asset. User manual, warranties and service protocols can make the product work longer. An information about the owner provides confirmation that the product is not stolen and support information on, for example, the availability of spare parts makes it easier to replace parts that are torn. The availability of information increases the possibility of reselling the product,” says Stefan Larsson.
That the DPP can also be used as a certificate of authenticity, which is assumed to affect the very large market for pirated copies, but also, for example, in the art world.
In the second project MCRS - Multicircular and Sustainable Manufacturing - participates in whatt.io together with Future by Lund, among others. To test a circular model, the 3Dprinting company is used Lostboyslab which is an autonomous factory that manufactures on demand, either self-designed products or as subcontractors to others. These are important parts to increase sustainability,” explains Stefan Larsson.
- Because Lostboyslab is available on the internet, it is a global business but with local manufacturing. The DPP can carry all the manufacturing information and it is conceivable that it should be possible to buy digital files so that the parts that are worn in local factories can be manufactured. If you work with many local factories on demand, you can eliminate warehousing and transportation. It is also easy to update the DPP to the latest and greatest version of the spare part or to adapt to local conditions so that you can use the materials on site.
In this particular project, Lostboyslab is printing speaker boxes for Infinite Acoustics 100% recycled materials that are a mix of industrial waste, car tires and recycled plastics. In the speakers, an NFC tag has been embedded in the plastic.
- In these speakers, DPP and 3D printing are used at a very high level. Each speaker is given a unique identity and becomes traceable from the time it is manufactured to the moment it is recycled and disassembled. It is important to think that if you are to become circular and environmentally friendly, you need to develop a cone friend mindset. At all stages of the product, information may be lost, but with DPP it is possible to link the digital to the physical reality. I think that through the speakers from Infinite Acoustics we are showing the way for the future of manufacturing!
Footnote: Whatt.io has made a detailed presentation of how they work with DPP. Here you can see the video where whatt.io's founder and CEO Stefan Larsson explains the basics of DPPs and how they are managed using whatt.io's cloud platform.
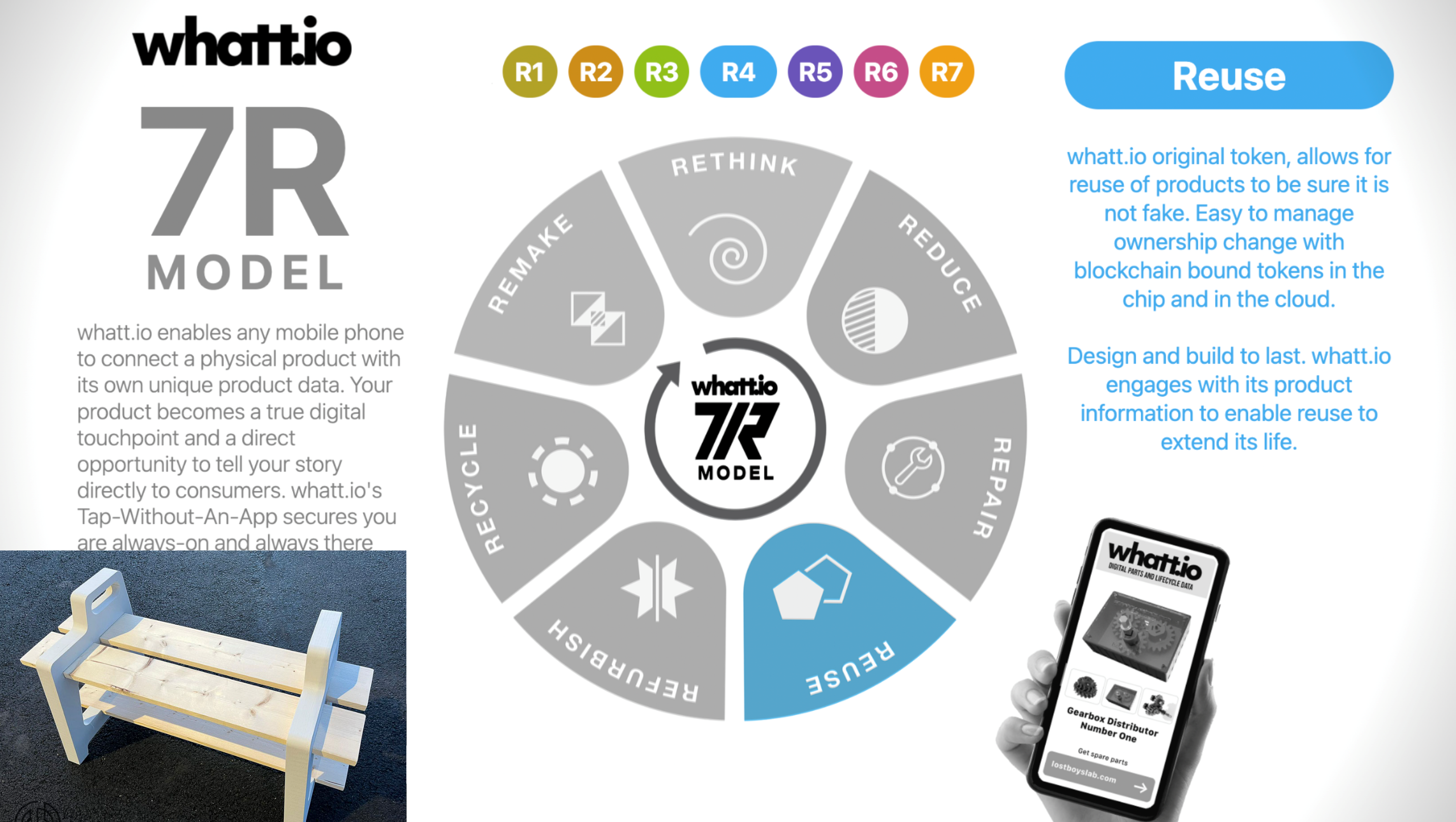